External failure costs are those that are incurred due to defects in products or services that are delivered to customers. In manufacturing, these costs can come from scrap, rework, or warranty claims. In service industries, they can come from customer churn or lost productivity.
Project management is all about anticipating and mitigating risks. And while there are many risks that are internal to the project itself, there are also external risks that can impact the project in a number of ways. One of the most significant external risks is the cost of failure.
External failure costs are the costs associated with defects that are discovered after the product or service has been delivered to the customer. These costs can include things like warranty claims, product recalls, and legal fees. These are discovered in appraisal cost analysis.
Causes of external failure costs
Failure costs can come in many forms, from the direct cost of repairing or replacing damaged equipment to the indirect cost of lost productivity. And while some of these costs are covered by insurance, others are not.
This is why it’s so important to have a plan for managing external failure costs.
One of the most common causes of external failure cost is scope creep.
This occurs when the scope of a project grows beyond what was originally planned, and can often lead to the project going over budget and behind schedule.
Other causes include inadequate planning, poor communication, and unrealistic expectations. By understanding the causes of this type of cost, you can be better prepared to avoid it in your own projects.
For example, External failure costs can be divided into two categories:
Direct Costs
Direct costs are the costs that are immediately incurred as a result of the failure, such as the cost of repairing damage to property.
Indirect Costs
Indirect costs are the costs that are not immediately incurred but may be felt later on, such as the loss of future business opportunities.
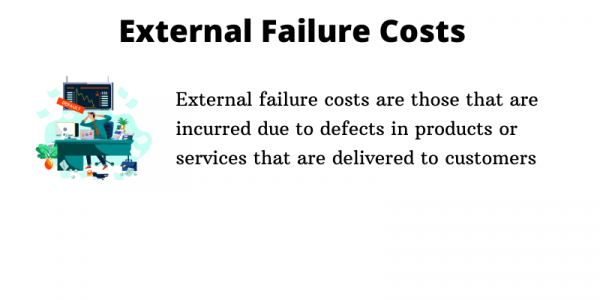
Managing External Failure Examples
In any project, costs incurred due to external failures can quickly add up and eat into the project’s budget. To avoid this, it is important to have an effective system in place for managing external failure costs.
One way to do this is to establish a process for identifying and classifying external failures. This process should be designed to ensure that all relevant costs are captured and accounted for. Once external failures have been identified and classified, it is then possible to develop strategies for mitigating or reducing these costs.
For example, you can:
- Encourage employees to report quality problems.
- Improve communications between departments.
- Require employees to document quality problems.
- Implement a quality improvement team.
- Conduct root cause analysis on all external failures.
- Take corrective action to prevent external failures.
- Monitor failure costs.
By having an effective system in place for managing external failure costs, you can help to keep your project on track and within budget.
Examples Of External Failure Costs
Lost productivity:
It is a major concern for any projects as it refers to the decrease in efficiency and output due to factors such as absenteeism, low morale, or ineffective use of time and resources. For example, a company that experiences a sudden increase in the number of employees taking sick leave or time off, may see a decline in productivity, which can negatively impact the bottom line.
Customer churn:
It refers to the loss of customers due to dissatisfaction with a product or service, the availability of competitive alternatives, or other reasons. For instance, a telecom company may experience high customer churn if it raises prices, decreases the quality of its network, or fails to keep up with new technological innovations. The loss of customers can lead to reduced revenue and profits, making customer churn an important metric to monitor.
Scrap costs:
These are associated with the production of defective or unusable products. They are a direct result of poor quality control procedures, inadequate training, or faulty machinery. For example, a manufacturing company that produces defective products due to these factors may incur significant scrap costs, which can eat into profits and impact the overall financial performance of the business.
Rework costs:
It refers to the costs associated with fixing errors or defects in a product after it has been produced. For example, a construction company may incur significant rework costs if it must fix structural problems in a building after it has been completed. These costs can be substantial, as they may include the cost of materials and labor required to fix the problem.
Damages to reputation or brand image:
These are critical assets that can be negatively impacted by product recalls, safety issues, and other scandals. For example, a car manufacturer that has several safety recalls may harm its reputation and brand image among customers, leading to decreased sales and revenue. Companies must take steps to prevent such issues from occurring and to quickly address any that do arise to minimize the impact on their reputation and brand image.
Lost sales and revenue:
Issues with a company’s products or services can result in lost sales and revenue, making it essential for businesses to maintain high-quality products and services. For instance, if a smartphone company releases a product with numerous bugs, customers may opt for competitors, resulting in lost sales and revenue. This can have a significant impact on the bottom line, making it important for companies to prioritize quality control and customer satisfaction.
Increased production costs due to rework and scrap:
When to fix or redo work, it leads to increased production costs due to wasted materials and labor. For example, if a garment manufacturer has to redo a batch of shirts because they were made too small, the cost of the extra labor and materials will increase production costs, eating into profits and affecting the overall financial performance of the business. Companies must take steps to minimize rework and scrap costs by implementing effective quality control measures and procedures, training employees.
Warranty claims
are one of the most common types of external failure costs. When a customer discovers a defect in a product, they can file a warranty claim with the manufacturer. The manufacturer then has to repair or replace the product, which can be costly.
Product Recalls
Product recalls are another type. If a product is found to be defective, the manufacturer may choose to recall the product. This can be a costly process, as the manufacturer may have to pay for the cost of shipping the defective product back to them, as well as the cost of replacement products.
Legal fees
Legal fees can lso be a significant external failure cost. If a company is sued for a defective product, it may have to pay legal fees, which can be significant.
These can have a significant impact on a project, as they can add up quickly. As such, it is important to be aware of them and take steps to avoid them.
Consequences Of External Failure Cost
There are a number of potential consequences of external failure costs in project management including internal failure cost.
These costs can include financial losses, damages to property, and legal liabilities. External failure costs can have a devastating impact on a project, and they can often be difficult to predict or calculate.
- It can lead to an increase in the overall cost of the project. This is because when external failure costs are incurred, they are typically charged at a higher rate than internal failure costs.
- It can also lead to delays in the project schedule. This is because it can take time to locate and remediate the issues that caused the external failure costs.
- Loss of confidence from stakeholders in the project. This is because external failure costs are often seen as a sign that the project is not being managed effectively.
External failure costs can have a significant impact on the success of a project. As such, it is important for project managers to be aware of the potential consequences of external
Tips to reduce external failure costs
External failure costs are often one of the largest types of costs for a company, so it is important to find ways to reduce them. Here are a few tips:
- Improve your process quality: This can help reduce the number of defects in your products or services.
- Increase your customer satisfaction: Happy customers are less likely to churn or file warranty claims.
- Invest in preventative maintenance: This can help reduce the number of costly Production failures.
By following these tips, you can help reduce your company’s external failure costs and improve your bottom line.
FAQs
What are the external failure costs?
External failure costs are those costs that are incurred when a product or service fails to meet the requirements of the customer or user. These costs can include repairs or replacement costs, as well as costs associated with lost productivity or revenue. External failure costs are typically much higher than internal failure costs, as they often involve third-party vendors or service providers.
How to manage external failure costs?
There are a few key things to keep in mind when it comes to managing external failure costs. First, it’s important to have a good understanding of the risks involved, and secondly, you need to have a plan for dealing with those risks.
Why are external failure costs important in project management?
External failure cost is an important metric because it can help organizations to assess the financial impact of a project failure. By understanding the external failure cost, organizations can make better decisions about whether to proceed with a project and how to minimize the risk of project failure.
What is measured in external failure costs in Project Management?
As it is represented by the costs that are incurred when a project fails to meet its objectives, it is typically measured in terms of lost revenue, lost productivity, and legal fees.