The appraisal cost is a type of conformance cost of the resources used to appraise the project deliverables and identify project issues and fixes. It includes the cost of all activities performed during project assessment, such as project audits, risk analysis, and inspection. In simple words, is the appraisal of the cost of fixing defects that are found during your project lifecycle.
In project quality management, appraisal cost is a significant resource that should be considered when making decisions about quality. It is the cost of all activities carried out to identify defects in the project’s product, process, or results.
This includes the cost of activities such as inspections, reviews, testing, and audits.
Also, it is a necessary cost incurred to ensure that the project is proceeding as planned and that any issues are identified and addressed in a timely manner.
This is an important part of project quality management and should be considered when making decisions about resource allocation.
When making decisions about quality, the appraisal cost should be weighed against the cost of not appraising, which includes the cost of defects that are not found and the cost of rework.
Appraisal Cost of Quality
Any organization starting a project must first understand the importance of appraisal costs in project quality management. While these costs can sometimes be high, they are essential to the success of any quality management effort.
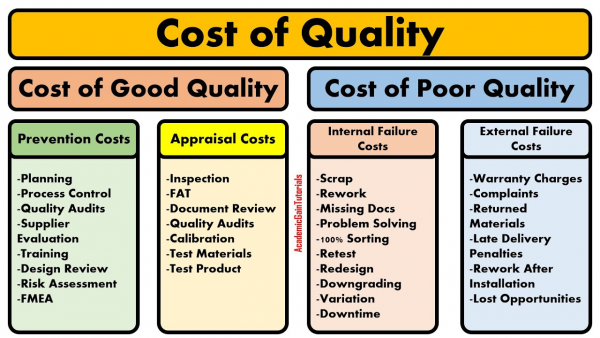
By investing in this cost, organizations can ensure that their projects are of the highest quality and that they are meeting customer expectations.
This allows for the early identification of problems and the implementation of corrective measures. By doing so, the project quality management team can avoid potential issues that could lead to costly repairs or rework.
For example, the cost of poor quality includes the costs of rework, corrections, and replacements that are needed due to defects. It also includes the cost of lost sales or revenue due to customer dissatisfaction. In addition, the cost of poor quality can also include the cost of increased warranty claims and legal fees.
By understanding and calculating these costs, the organization will be able to set a budget for the project that takes into account all necessary factors, including the costs of personnel, time, training, and more.
When organizations often overlook the importance of appraisal costs and end up going over budget on their projects. This can lead to project delays, cost overruns, and ultimately, poor project quality.
By understanding the importance of these costs and how to calculate them, organizations can avoid these problems and ensure that their projects are completed on time and within budget.
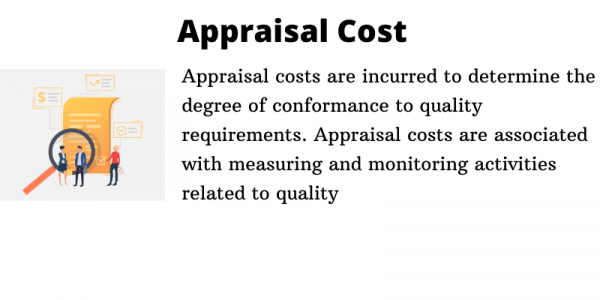
9 Examples Of Appraisal Costs In Projects
There are many different ways to incur appraisal costs.
Generally speaking, for example, appraisal costs can be incurred when hiring a third party to assess the quality of a project. Appraisal costs can also be incurred when conducting internal audits of a project. Quality assurance appraisals seek to identify potential problems with a project and take steps to prevent them from occurring. Quality control appraisals monitor a project for compliance with quality standards. These appraisals are essential for ensuring that a project meets its quality objectives.
- Inspections
- FAT
- Document Review
- Quality Audits
- Calibration
- Test Product
- Test Materials
While these costs can be significant, they are often necessary in order to ensure that a project meets its quality objectives. Therefore, it is important for project managers to be aware of the different types of appraisal costs that can be incurred during a quality management process.
Calculating Appraisal Cost
To understand this, let’s take a super quick and easy example of a coffee shop.
- Andy started this coffee shop in a small city. During the first month, the demand arose and people started to recommend it in big quantities. During the second month, Andy couldn’t help making it the good quality that initially gave him fame. And people started to complain about the quality of the shop. That month Andy sold 600 where 200 were returned by the customers.
- Due to this, Andy was spending more than expected and customer satisfaction was going low. So he decided to employ a Quality Control Assistant who was in charge to check that every coffee was at the high-quality standards required.
- Suppose the salary of this Quality Control Assistant was $400 per month and the cost related to the testing and inspection of every coffee was $100.
- In the end, thanks to the Quality Control Assistant, sales rose and customer satisfaction increased significantly.
But what about the formula?
Using this example, the total appraisal cost of quality could be calculated by
Total Appraisal Cost = The Quality Control Assistant $400 + The cost related to the testing and inspecting is $100
$400 + $100 = $500
I.e: the total appraisal cost is $500
Difference Between Appraisal Costs And Prevention Costs
The main difference between prevention costs and appraisal costs is that prevention costs are incurred before a defect occurs while appraisal costs are incurred after a defect has occurred.
- Prevention costs are incurred in order to avoid defects from occurring in the first place.
- These costs are typically incurred during the design and development phase of a product or service.
- Some examples of prevention costs include quality training for employees, investing in better quality control methods, and setting up a quality management system.
- Appraisal costs, on the other hand, are the costs incurred to identify defects after the product or service has been completed.
- These costs are typically incurred during the testing and quality assurance phase of a product or service.
- Examples of appraisal costs include inspecting products for defects, testing products to see if they meet quality standards, and sorting products that are defective from those that are not.
While prevention costs are typically higher than appraisal costs, they can save your company money in the long run by avoiding the need to fix defects later on.
In addition, prevention costs can also help to improve the quality of your product or service, which can lead to higher customer satisfaction.
Advantages and Disadvantages When Doing Appraisal Costs For Your Project
Appraisal costs are important in project quality management because they can provide insights into the effectiveness of quality control measures.
However, appraisal costs can also be a significant expense for an organization, particularly if they are outsourced.
Advantages | Disadvantages |
---|---|
Appraisal costs can be advantageous because they can help identify problems early on in the project lifecycle. This can save money and avoid legal problems down the line. | They can be time-consuming and complex, which can lead to delays in the project, and sometimes inaccurate, which can lead to unexpected expenses. |
Additionally, appraisal costs can improve communication between project managers and stakeholders. | If appraisal costs are outsourced, there can be a lack of control over the process. Another potential downside is that they can add extra work for the project manager. |
Tips To Reduce The Appraisal Cost
As a project manager, one of your main objectives is to complete your project within the set budget. Unfortunately, this isn’t always possible.
There are a number of factors that can lead to project cost overruns, one of which is appraisal costs.
Also, as project quality management professionals know, the cost of appraisals can quickly add up.
There are many factors to consider when appraising a project, and the cost of appraisals can quickly add up.
- One way to reduce appraisal costs is to use sampling techniques. This involves selecting a small number of randomly chosen items from a batch and appraising them. This can be done for a variety of quality characteristics, such as dimensions, weight, or function. By only appraising a small number of items, you can save on both the cost of the appraisal itself and the cost of rework if the batch is found to be defective.
- Another way to reduce appraisal costs is to use inspection by variables. This is a method of quality control in which items are inspected for a single quality characteristic, such as length or width.
Here are some other general tips to help you reduce the cost of appraisals:
- Reduce the number of appraisers on the team
- Conduct appraisals remotely
- Use automated tools to support the appraisal process
- Leverage existing quality data to reduce the need for new appraisals
By following these tips, you can help reduce the cost of appraisals and ensure that your project quality management process is as efficient as possible.
FAQs
What are Appraisal Costs in Project Management?
Appraisal costs are the costs associated with assessing the quality of the project deliverables. They can include things like quality assurance tests, project audits, and independent reviews. appraisal costs can quickly add up and eat into your project budget.
How can Appraisal cost be used for?
The appraisal cost can be used to identify problems, assess the impact of potential fixes, and compare the cost of different approaches to quality.
Why is appraisal cost important for your project?
By understanding and calculating these costs, the organization will be able to set a budget for the project that takes into account all necessary factors. appraisal costs include the costs of personnel, time, training, and more.
What is Project Quality Management in Appraisal Costs?
In Conformance Cost, Project quality management is the process of ensuring that a project meets all the required quality standards including quality planning, quality assurance, and quality control.